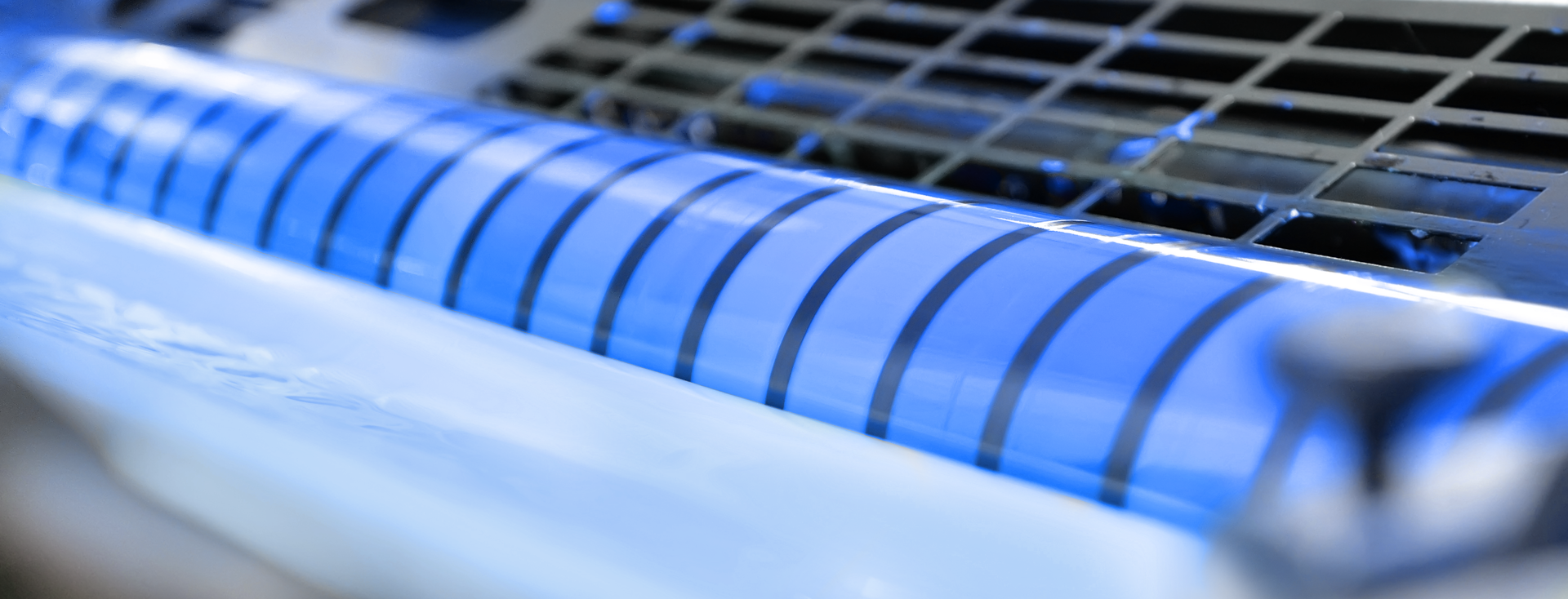
Offset printing
Quality assurance by means of interfacial chemical investigations of moistening agents, inks and printing plates
As a planographic printing method, offset printing is based on the different wettability of the printing and non-printing areas of the exposed printing plate by the ink. Knowledge obtained from scientific investigations of the interface of the moistening agents used, the inks and the printing plate contribute to a high-quality printing result.
Wetting of the non-printing areas by moistening agent
In the two-stage offset printing process, a water-based moistening agent is first applied to the printing plate. This wets only the non-printing areas and therefore prepares for later, selective wetting of the printing areas by the ink.
The surface tension of the moistening agent must be low enough to wet the non-printing areas. However, if it is too low, it can also partially wet the printing areas and form an emulsion with the ink when it comes into contact with it. Both lead to an unsharp printed image. Measurement of the surface tension of the moistening agent with our tensiometers is therefore an important step in quality monitoring.
With moistening agents which contain surfactants, it must be borne in mind that surfactants only reach a newly formed surface after a certain time. In the case of highly dynamic offset printing, the surface tension can therefore be considerably higher than when the moistening agent is in the quiescent state. Dynamic bubble pressure tensiometers measure the value of the surface tension as a function of the surface age right down to a few milliseconds.
Wetting of the printing areas by ink
The ink exhibits the opposite behavior to the moistening agent on the printing plate in that it wets only the printing areas. An important factor here is that the ink has a hydrophobic character, namely a low surface tension while also having a low surface polarity.
The ink paste is applied in order to carry out the measurement. Drops of different test liquids are then dispensed onto the ink layer and optically analyzed. The measurement gives the surface free energy and its polar and disperse parts. These measurements are important parameters for the wetting of energetically different areas of the printing plate.
The interfacial tension between moistening agent and ink should be as high as possible in order to ensure a distinct interface. This quantity can be calculated from the measurement data obtained from the moistening agent and the ink.
Wettability of the printing plate
An overall interfacial chemical image of the printing process is obtained if the wettability profile of the printing plate is also created. The printing and non-printing regions are areas of lower and increased surface free energy and polarity which can likewise be characterized by means of contact angle measurements.
Our mobile contact angle measuring instruments are used for ensuring the quality of an exposed printing plate and enable the measurement to be carried out non-destructively directly on site.
Overall interfacial chemical image for process optimization
If moistening agent, ink and printing plate have been characterized, then adhesion and wetting enthalpies can be calculated for all wetting processes and phase changes which occur in the printing process. The resulting overall surface chemical image enables the components concerned to be optimized separately to produce a high-quality printing result.