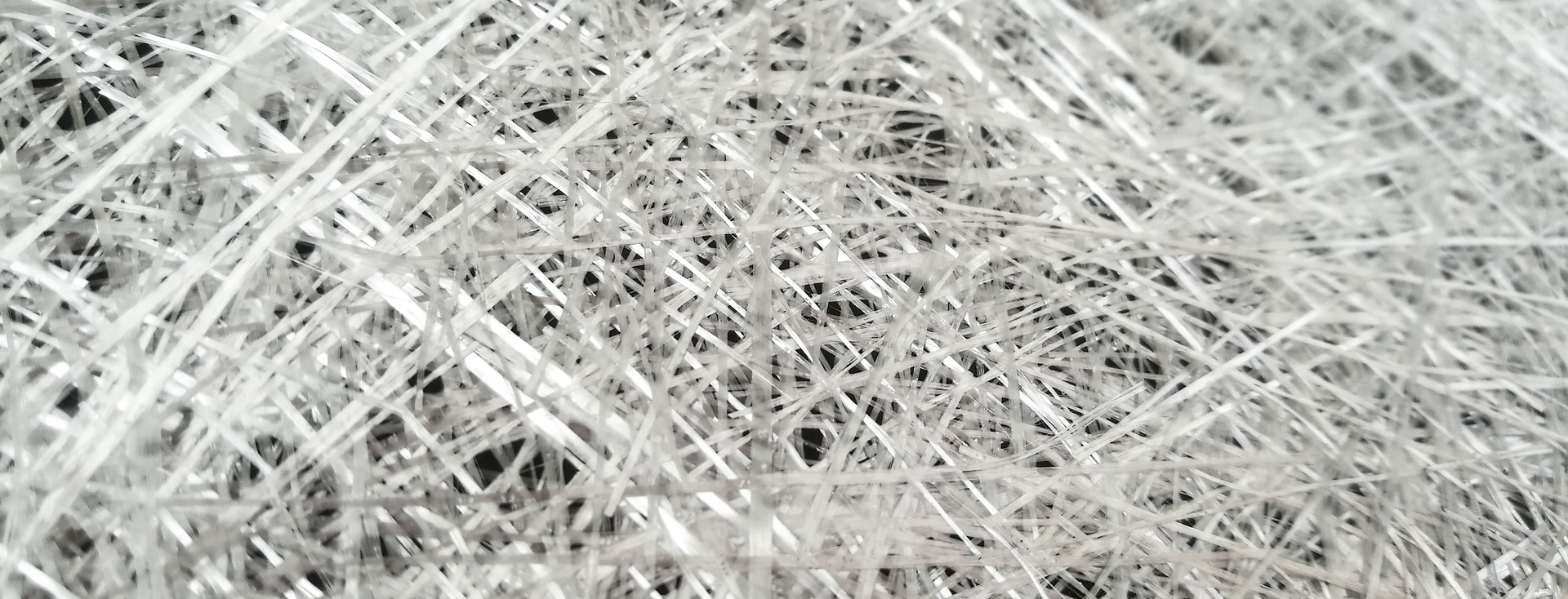
Coating of fibers
Methods for monitoring wetting, adhesion and cleaning
When coating natural and synthetic fibers, wetting and adhesion to the surface as well as the coating thickness are decisive factors for high product quality. Our measuring instruments are used in the quality control of fiber-coating processes in order to avoid air pockets and irregular or unstable coating.
Typical fiber-coating applications
- Pre-coating of carbon, glass and natural fibers for embedding in fiber-reinforced composites
- Hair dyeing and temporary coating to make combing easier
- Temporary protection of fibers before weaving (sizing)
- Water-repellent coating on technical textiles
- Coating on glass fibers to improve elasticity and breaking strength
Wetting and adhesion
The wetting and adhesion between fiber and coating result from the interaction of the two components at the interface. A combination of methods between contact angle measurement for the fiber and measurement of the surface tension for the coating is therefore ideal.
The wettability of the fiber by the coating can be measured directly in the form of the contact angle between the components involved. If, on the other hand, fiber and coating liquid are investigated separately, the two products can be matched to one another. A rule of thumb says that the coating provides optimum wetting when its surface tension is less than the surface free energy of the solid.
The surface polarity of the two phases is also determined in order to calculate the adhesion in the form of work of adhesion. The adhesion is stronger and has better long-term stability the more similar the pro-rata polar forces of the two phases at the surface.
For uniform fibers such as hair, carbon and glass fibers, we recommend that the contact angle and surface free energy be determined using a single-fiber tensiometer. With irregular fibers, it is advisable to use an optical contact angle measuring instrument with microscope lens and picoliter dosing.
The surface tension of the liquid coating is determined using the ring or plate method. Our tensiometers use this method of measurement with fully automatic or semiautomatic sequences.
Coating thickness
Surfactants reduce the surface tension in the coating bath. When a fiber moves through the bath quickly, the surface tension at the point of exit is higher, as fewer surfactant molecules remain on this newly formed surface. As a result of the difference in tension, a force acts along the fiber, a process known as the Marangoni effect. This effect is specifically used to increase the coating thickness.
Surfactant molecule clusters (micelles) in the coating bath diminish the effect, as molecules quickly migrate from the micelles to the new surface and reduce the surface tension. The critical micelle concentration (CMC) of the surfactant can be measured precisely and fully automatically with a force tensiometer in order to guarantee the use of surfactant with the right concentration.
Coating dynamics
Coating processes usually run at high speed. Bubble pressure tensiometers carry out the appropriate measurements of the dynamic surface tension. These are capable of measuring the value of the surface tension a few milliseconds after a new surface has been produced and therefore realistically represent the process conditions.
Foam prevention
Foam can be produced due to the high dynamics of the coating process. Foam bubbles adhering to the fiber mean a loss of strength and regularity of the coating. The foamability of the coating and the effect of foam inhibitors (anti-foamers) can be checked and the product quality improved with our foam analysis instruments.