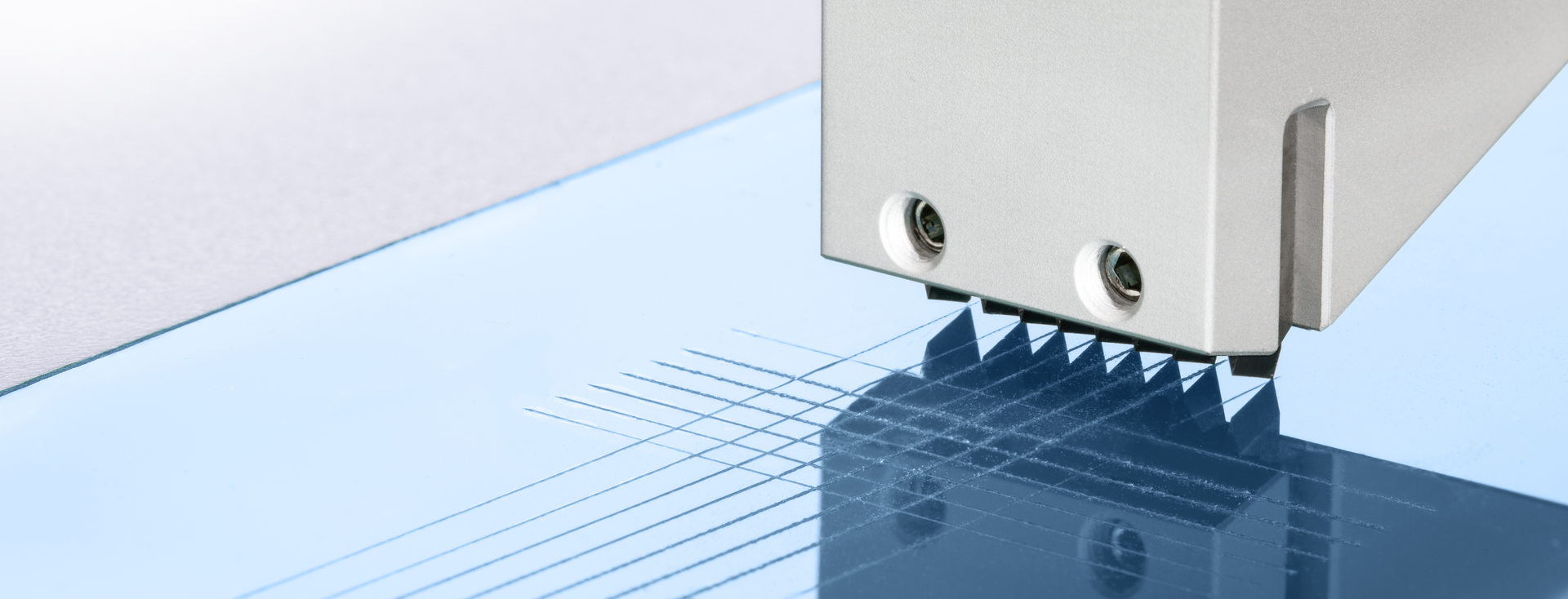
Moving Beyond Cross Hatch: The Stood-Up Drop® Technique as a New Route to Assess Coating Adhesion
Correlating the dewetting angle with ISO2409:2020 test results
Authors: Andrew Mellor (KRÜSS), Petra Della Valentina (BYK), Dennis Winkler (Plasmatreat GmbH)
The humble contact angle measurement is an essential part of any coatings specialist’s toolbox, used to quantify wettability, (re)coatability, defect occurrence, cleanliness, and more [1]. For decades, a considerable effort has been invested in determining the relationship between contact angle and coating adhesion. Observations reveal that this approach works well for some systems but not at all for others. Because of this, contact angle measurements are often supported – or replaced – by destructive methods the most well-known of which being cross hatch/crosscut (tape), and pull-off (dolly) tests [2]. While destructive tests are commonplace across many industries, like automotive, aerospace, electronics, marine, packaging, etc., their use is not ideal due to issues with subjectivity, expertise required, quantification of results, and the time to measure (typically 24 – 48 hours, depending on curing time of the coating) [3].
In this work, we demonstrate the importance of choosing the most suitable type of contact angle when assessing adhesion. Specifically, the new KRÜSS Stood-up Drop® method, which captures dewetting behavior, is shown to quickly generate results that reliably predict adhesion performance of a coating on different substrates.
Background
Wetting and dewetting
It is commonly assumed that, as inverse processes, wetting and dewetting have a symmetrical relationship. However, the difference between so-called advancing and receding contact angles, known as contact angle hysteresis, is direct evidence to the contrary (see Fig. 1). In a theoretical sense, an atomically flat, chemically homogeneous surface is expected to exhibit symmetrical wetting/dewetting properties; yet, in reality, such conditions are rare. During wetting of water on real surfaces, hydrophobic elements of the substrate act as a barrier to advancement of the contact line, causing the water’s contact angle to increase as it encounters these areas (see Fig. 1, left).
Conversely, during dewetting it is the hydrophilic areas of the substrate that act as a barrier to contact line recession, thereby decreasing the contact angle of water (see Fig. 1, right). Differing chemistry of hydrophobic and hydrophilic groups is therefore what gives rise to hysteresis. Therefore, when applying contact angles, it is important to consider whether the characteristic in question is best described by wetting or dewetting.
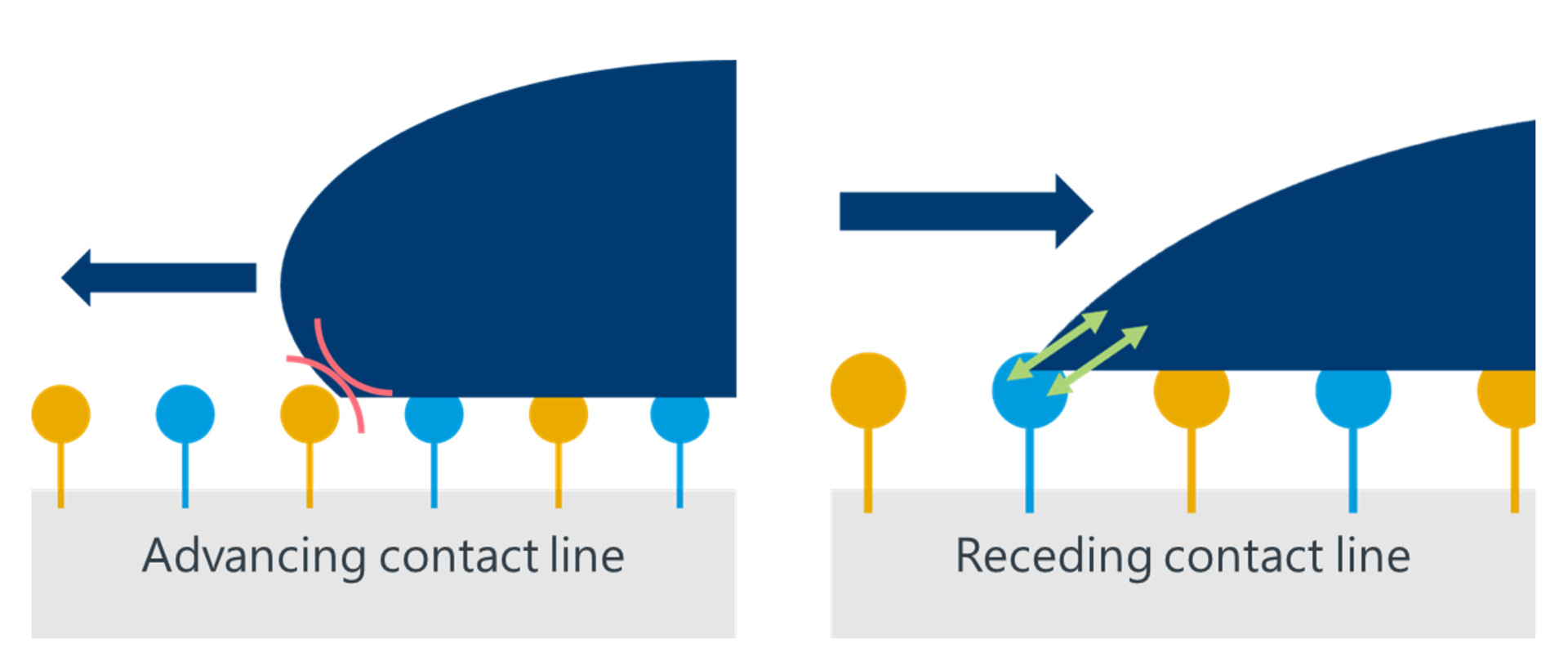
Capturing wetting and dewetting with contact angles
A traditional contact angle measurement involves depositing a liquid drop onto a surface and allowing it to spread out until it reaches equilibrium shape. The shape is then quantified by measuring the angle between liquid and solid at the three-phase point. Because the drop is measured at rest after spreading out (advanced), this value is described as a recently advanced contact angle (RACA). The frequently used term “static contact angle” is not appropriate because it says nothing about the “history” of the drop.
As with advancing contact angles (recorded from expanding or moving drops), RACAs correlate well with wetting-dependent phenomena like coatability, dispersibility, or absorbability. On the other hand, dewetting-related aspects like adhesion, roll-off, or ‘crawling’, are best characterized by so-called recently receded contact angles (RRCAs), where drops are measured at rest after being retreated (receded) from the surface. For clarity, RACAs and RRCAs will hereafter be referred to as wetting angles and dewetting angles, respectively.
While wetting angles are easily measured with traditional contact angle equipment, dewetting angles prove much more difficult. In practice, dynamic receding contact angles are the most commonly used tool for simulating dewetting. However, owing to the relative complexity and time-consuming nature of such measurements, they are not widely employed [4, 5]. Indeed, dynamic contact angle measurements may take several hours to complete and often fail to produce receding contact angle values at all [4, 5]. The Stood-up Drop has been specifically designed to dramatically accelerate dewetting angle measurements while delivering user-independent results.
This work focuses on clarifying the link between the different types of contact angle and adhesion performance by testing several different systems:
1. Solvent-based clearcoat on four metal substrates
2. Solvent-based clearcoat on four polymer substrates
3. 2K water-based topcoat on plasma-activated polypropylene
4. Melamine clearcoat on polyester basecoat (containing BYK-SILCLEAN 3700 as additive)
An additional five systems were tested, but, for brevity, their results are not detailed in this report. An overview of all nine systems is given in Table 1 at the end of the Results section.
Experimental section
Wetting and dewetting angle measurements
All contact angle measurements were performed with doubly distilled ultrapure water using a KRÜSS DSA100 contact angle instrument. Each reported contact angle represents the average of at least 10 repeat measurements.
The wetting angle was measured with a KRÜSS Liquid Needle. In this method, a sufficiently large drop (2 µL in this study) is produced by means of pressure dosing, whereby the dosing dynamics are adjusted so that no withdrawal movement occurs after dosing, i.e., no dewetting takes place. [6]
The KRÜSS Stood-up Drop is also based on pressure dosing but does the exact opposite: it applies a small drop (0.4 µL in this study) to the sample with high momentum, causing it to spread out flat at first and then contract in a split second due to surface tension. This is how dewetting is deliberately induced (see Fig. 2).
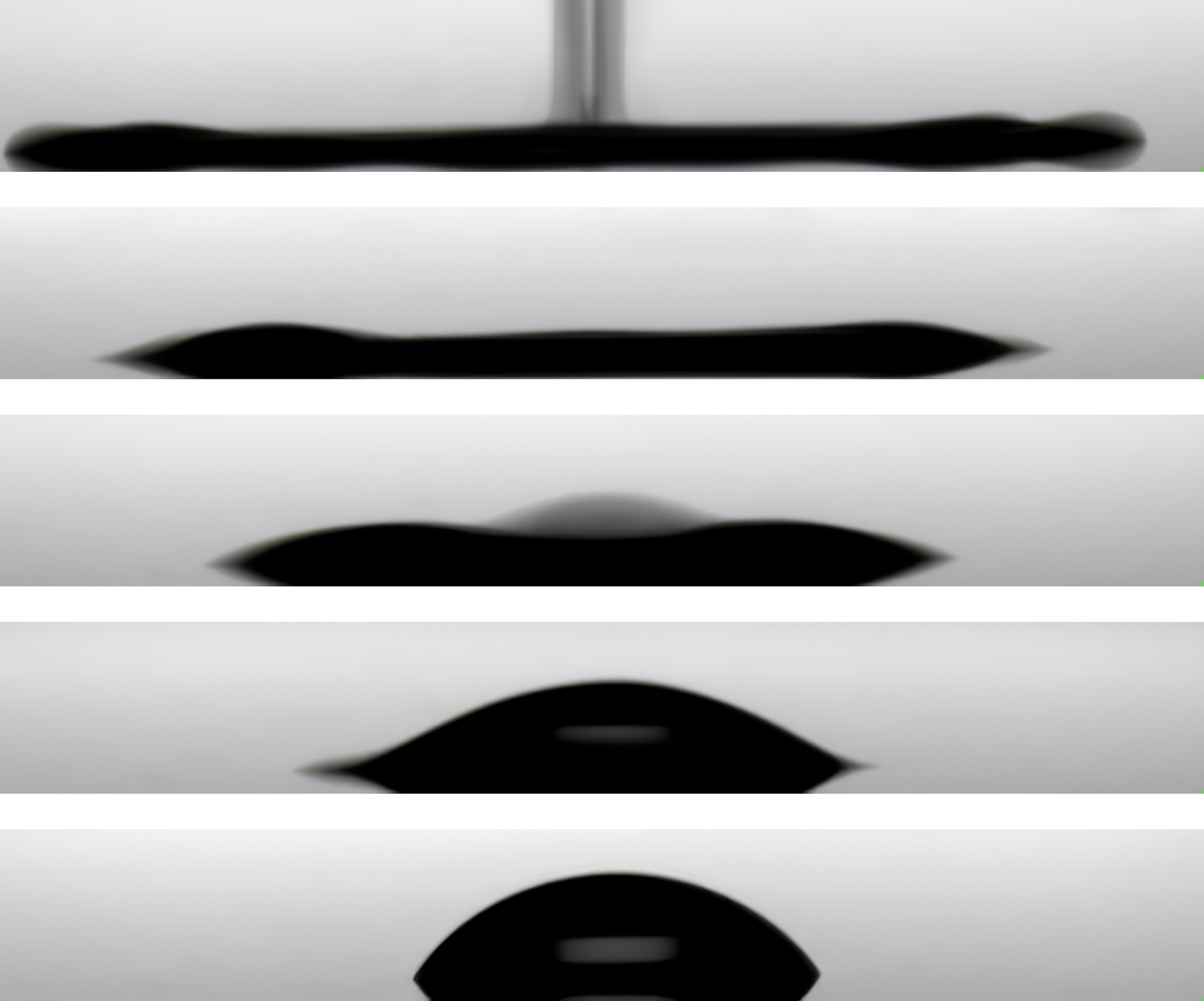
Samples and sample preparation
Coatings, substrates, and additives were provided by BYK. Adhesion tests were performed using a BYK-Gardner cross hatch adhesion test kit, following ISO2409:2020, where 0 indicates the highest adhesion level and 5 the lowest [2].
Atmospheric plasma activation was carried out using a generator (FG5001S), control unit (PCU-M), rotary nozzle (RD1004), and nozzle head (22826, 14°) from Plasmatreat GmbH. Process parameters, including dwell time, plasma power, and nozzle-substrate distance were systematically varied to control plasma exposure levels.
Results
Different polymer substrates
In a first series of tests, wetting and dewetting angles of water drops were measured on PP, PMMA, ABS, and PP substrates. Afterwards, a solvent-based clearcoat (Setal 1715) was applied to each substrate and left to cure for 48 hours. Adhesion of the clearcoat to each substrate was tested via the tape test and compared to both wetting and dewetting angles (see Fig. 3). Adhesion performance of the clearcoat varied greatly with substrate, following the trend PA>PMMA>ABS> PP. Despite this, no significant difference in wetting angle was observed between PA, PMMA and ABS. In contrast, dewetting angles showed a clear (negative) correlation with adhesion, and a linear fit of the data gave a correlation of determination, R2, of 0.94. The R2 value is a measure of the strength of the correlation, with 1 being the maximum value.

Different metal substrates
In a second series of tests the same solvent-based clearcoat (Setal 1715) was applied to a range of metal substrates, namely normalized steel (N-Steel), Zn-steel, standard aluminium (Al) and high purity aluminium (Q-panel Al). Prior to coating, wetting and dewetting angles were measured and, as before, the clearcoat was left for 48 hours to cure before performing tape tests. Standard Al and Zn-steel showed similar adhesion performance (1 on ISO scale), as did high purity Al and N-steel (2 on ISO scale). Again, changes in wetting angle were seemingly independent of adhesion performance, whereas dewetting angles followed the adhesion well, with a linear fit giving an R2 of 0.85 (see Fig. 4).
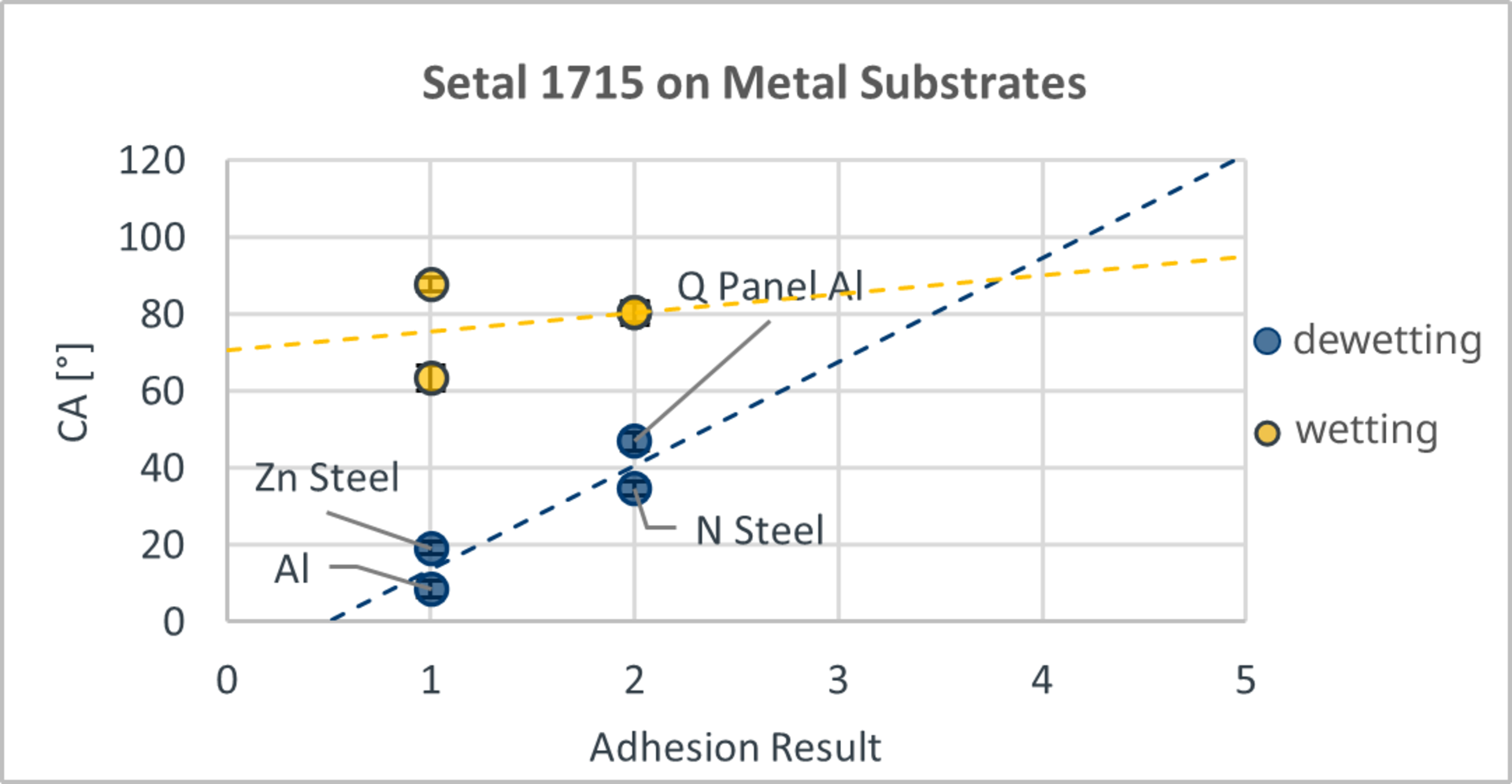
Different plasma activation levels on PP
Next, wetting and dewetting measurements were performed on PP substrates following increasing exposure to atmospheric plasma. Afterwards, a 2K water-based topcoat was applied to each PP substrate, and, following the 48 hours curing time, adhesion performance was measured via tape test. A clear improvement in adhesion performance was observed with increasing plasma exposure, and a range of adhesion levels was realized (1, 2, 3 and 5 on ISO scale) by varying plasma intensity/exposure time. In this case, both wetting and dewetting angles showed a clear correlation with adhesion performance. A linear fit revealed RRCA to have the highest R2 of 0.98 (vs 0.82) (see Fig. 5).
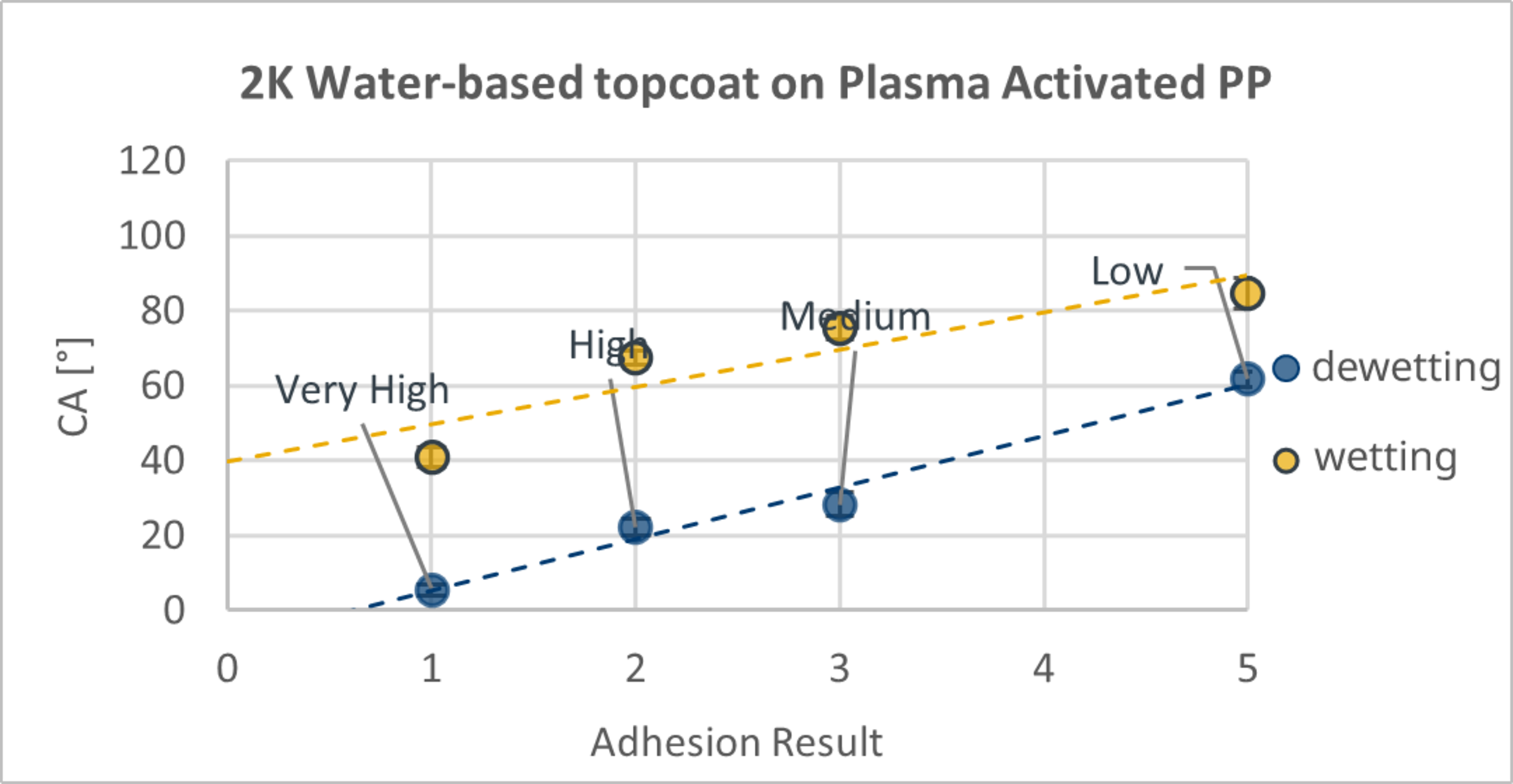
Different basecoat formulations
In a final series of tests, wetting and dewetting angles were measured on samples of a cured polyester basecoat containing BYK-SILCLEAN 3700 as easy-to-clean additive. Wetting and dewetting angles were measured, and a melamine clearcoat was then applied and cured for 48 hours before performing tape tests. As the additive concentration in the basecoat layer was increased a corresponding decrease in adhesion performance was observed. Similar to the plasma-activated PP samples, changes in both wetting and dewetting angles correlated with changes in adhesion performance (see Fig. 6), with dewetting angles yielding a superior R2 of >0.99 (vs 0.85).
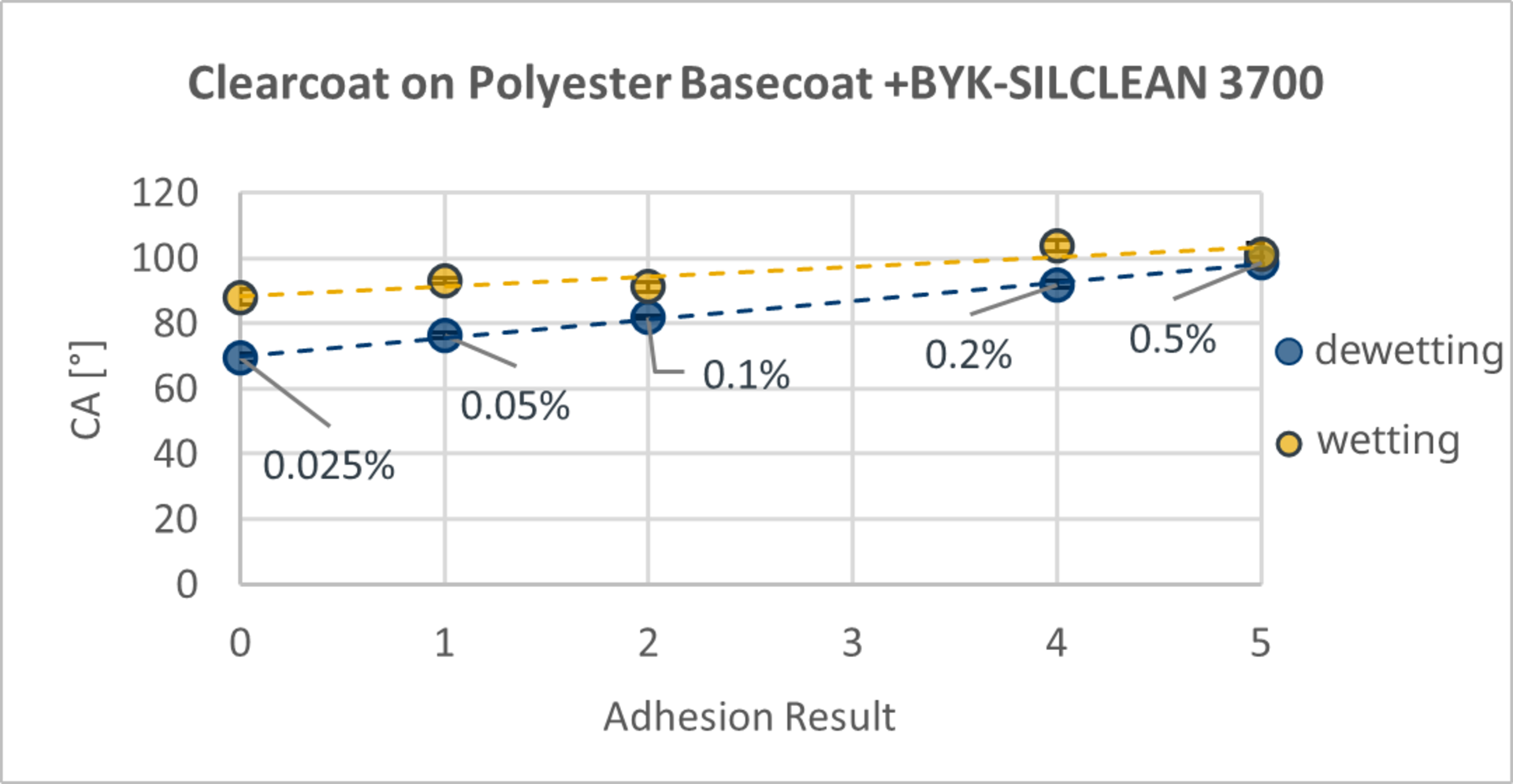
Though a correlation of the wetting angle with adhesion was observed in this case, the change for the first three samples (0.025%, 0.05% & 0.1%) was close to being within standard deviation of each other. In contrast, dewetting angles showed a much more pronounced variation (~30°) across the full adhesion scale.
Additional test series with varying materials or treatments
The above-described procedure was repeated for five further coating/substrate systems, utilizing either plasma exposure or additive concentration to vary adhesion. In the additional tests, a correlation with adhesion for both wetting and dewetting angles was observed, with the notable exception of plasma activated ABS, where wetting angles did not vary with adhesion. For ABS, only a small increase in adhesion could be realized through plasma exposure, from ISO 1 to ISO 0. R2 values for these samples are omitted from the table as only two data points were recorded in each case. Interestingly, for plasma activated PA substrates wetting angles showed superior or equivalent correlation with adhesion performance as compared with dewetting angles.
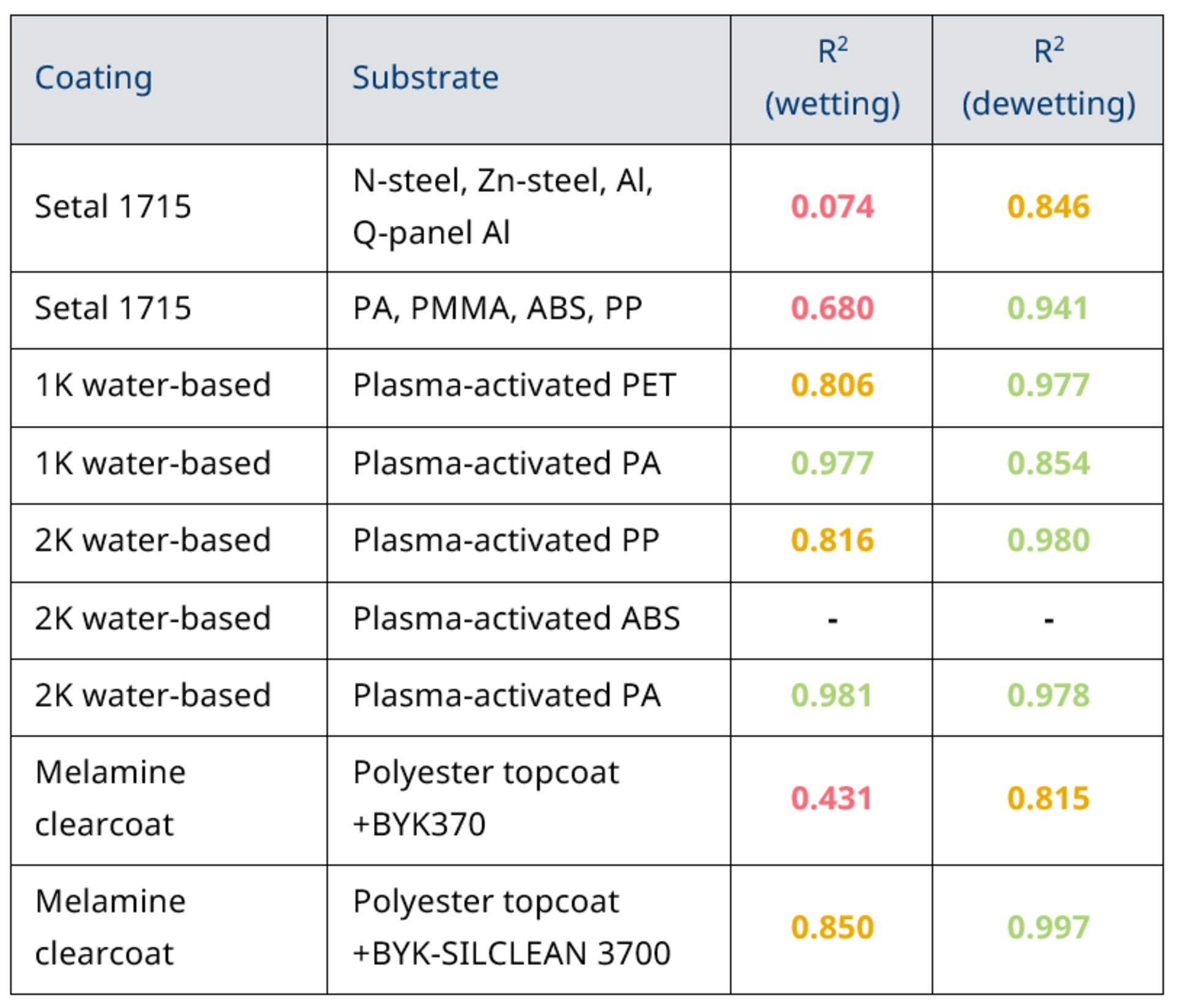
Summary
In this work, a clear, robust correlation between contact angle and coating/substrate adhesion has been demonstrated for a range of coating and substrate chemistries, as well as for additive modified and plasma activated substrates.
In all cases, dewetting angles correlate well with adhesion performance, and in 7/9 systems tested dewetting angles gave a more reliable correlation than wetting angles. To illustrate, linear fittings were applied to each data set and R2 values were compared. Across all 9 systems, dewetting angles gave an average R2 of 0.92, indicating a very reliable correlation, whereas wetting angles gave a much lower average R2 of 0.70. In 4/9 test cases wetting angles did not correlate with adhesion at all. This result aligns with the common observation that traditional (wetting) measurements only work for some systems as a method to gauge adhesion.
The need for a fast, objective, quantifiable and easy to use method for assessing adhesion performance is well known across many industries [7]. From this work, application of the Stood-up Drop method for measuring dewetting angles has shown to hold great promise as a route to reducing reliance on destructive adhesion tests. As absolute adhesion strength values cannot be determined from dewetting angles, destructive tests will likely continue to play a role as a final-step assessment for coating performance. However, the extent of destructive tests during formulation and troubleshooting can be significantly reduced through this approach.
Literature
- [1] A. Marmur: Solid-surface characterization by wetting. Annu. Rev. Mater. Sci., 39(1), 2009, 473-489
- [2] International Organization for Standardization. 2013. Paints and varnishes - Cross-hatch test. ISO Standard No. 2409:2020.
- [3] A. S. Maxwell: Review of test methods for coating adhesion. NPL Report MATC (A)49, 2001.
- [4] T. Huhtamäki, X. Tian, J. T. Korhonen, R.H.A. Ras: Surface-wetting characterization using contact-angle measurements. Nat. Protoc., 13, 2018, 1521-1538.
- [5] C. W. Extrand: Contact angles and their hysteresis as a measure of liquid-solid adhesion. Langmuir, 18(21), 2002, 7991-7999.
- [6] M. Jin, R. Sanedrin, D. Frese, C. Scheithauer, Th. Willers: Replacing the solid needle by a liquid one when measuring static and advancing contact angles. Colloid and Polymer Science 294(4), 657-665, DOI 10.1007/s00396-015-3823-1 (2016).
A summary of this article is presented in our Application Report AR278. - [7] N. Inagaki, K. Narushima, T. Taki: Surface modification of polymers by plasma treatments for improving adhesion. Surf. Coat. Technol., 98(1-3), 1997, 1205-1210.
BYK® and BYK® SILCLEAN® are registered trademarks of the BYK group.
We would like to thank BYK® and Plasmatreat for the successful cooperation in this project.