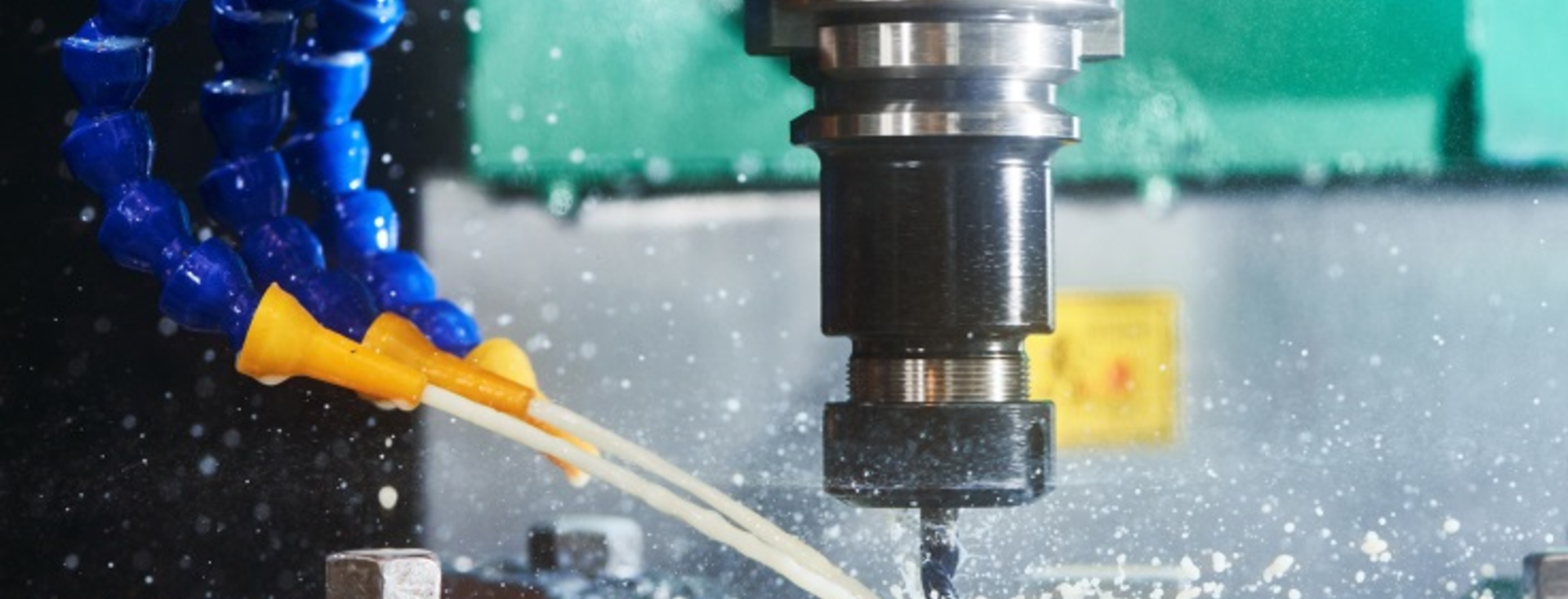
A reliable method for monitoring the aging and performance of cooling liquids used in machining processes
Microbubbles and foaming behavior of fresh and used cooling liquids
In many areas of industrial manufacturing, cooling liquids are essential to ensure the machining process, the quality of produced parts, and the lifetime of machines. Among other things, those liquids are designed to have maximum air release properties and minimum foamability. However, during usage such liquids are subject to change, resulting in a reduced cooling efficiency. Our costumer wanted to monitor this behavior in order to optimize grinding processes at a large manufacturing site.
After a series of attempts to differentiate between fresh and used cooling oil based on typical standard chemical lab characterizations and manual foam tests, our costumer contacted us for further consulting and support on this project. The application report presented here contains a foam study on fresh and used samples of two different cooling liquids, carried out at the KRÜSS Applications & Science Labs. We found a measurement procedure which finally facilitated a reliable and highly reproducible monitoring of the change of such cooling liquids.
Background
At manufacturing sites our client produces all kinds of metal parts such as bearings. Important manufacturing steps in metal working are machining with water or oil based cooling liquids. Among other things such liquids are to one main factor to guarantee the mechanical and physical product quality.
Foams and air in water/oil dispersions have a reduced cooling efficiency (heat capacity) and an unfavorable flow behavior in comparison with pure liquids. This is why cooling liquids are designed to show minimum foamability along with high air release properties. However, cooling liquids change with time, which could result in reduced air release properties, i.e. in a higher content of dispersed air. These effects of usage decrease the cooling.
In some production sites several machines are connected to a central supply system containing up to 100,000 L of cooling liquid. Thus it is cost effective to know precisely when the liquid needs to be modified or even exchanged. For this reason and, more importantly, to sustain high quality standards, our client searched for an experimental method to monitor possible effects of usage of the cooling liquids when they are used. Simple visual inspection was not capable in differentiating fresh from used oil (see Figure 1). Also more sophisticated methods including common chemical lab analytical methods could not reveal any differences between fresh and used oil.
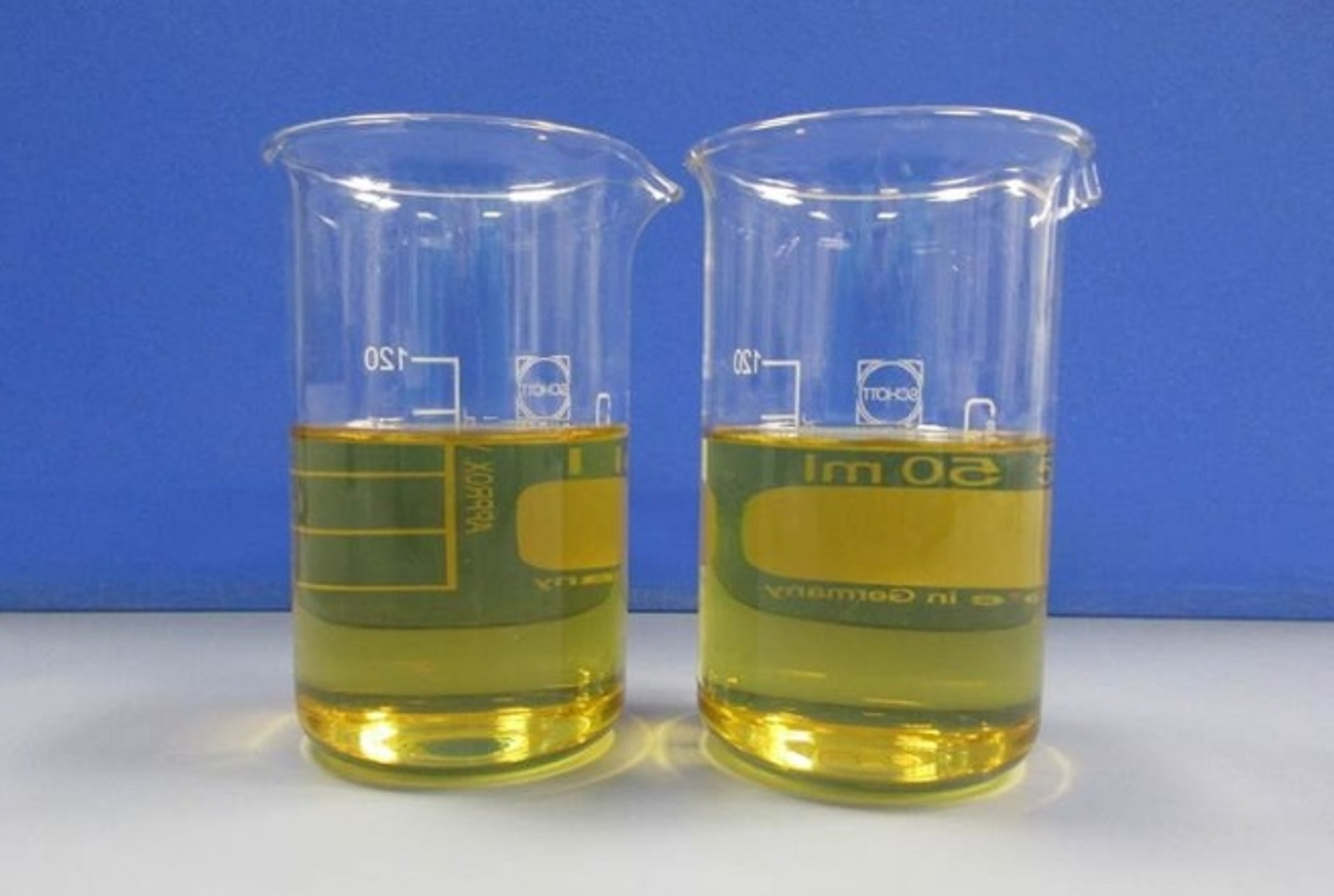
As air dispersed in a liquid can be related to foam, our costumer initially did foam studies by manually shaking glass columns as foaming method. However, no reproducible and thus reliable data could be collected, in particular due to the manual handling of different operators. That was the point when our client contacted KRÜSS for consulting service and more sophisticated equipment in terms of foam analysis.
Experimental part
In this study we investigated two cooling liquids based on highly refined, low viscosity mineral oils from two different suppliers. In this report we anonymize the products and refer to them with Type A and Type B.
All experiments have been carried out with our Dynamic Foam Analyzer – DFA100 (for further details about experimental methods we refer to [1],[2]). The DFA100 offers two automated methods for foaming: stirring and sparging. Cooling liquids are designed to have highest air-release properties along with lowest foamability, i.e. they are low-foamers. In general, sparging is the preferred foaming method over stirring for low-foamers as his method is capable of generating much more foam and thereby guaranteeing a higher relative accuracy of the collected data. Indeed, pretests with the samples using stirring as foaming method did not yield sufficient foam volume.
When using sparging as foaming method the amount of produced foam does not necessarily need to increase linearly with the gas flow rate of the introduced gas. Therefore, pretests can help to find the gas flow which produces the largest amount of foam. For the samples investigated here, the maximum foam volume was generated by the highest possible flow rate of 1 L/min.
Finally, the following experimental conditions were used for best comparison of the samples:
- Temperature: 20-27 °C
- Sample volume: 100 mL filled in by prewetting the inner wall of the glass column using a 100 mL glass pipette
- Frit: disposable filter frit (FL4520) which reduces the cleaning work between separate runs to a minimum
- Sealings: Viton (FL4506)
- Gas: air
- Flow rate: 1 L/min
- Light source: IR light source with 15% intensity
Measurements were carried out as programmed in KRÜSS ADVANCE Software:
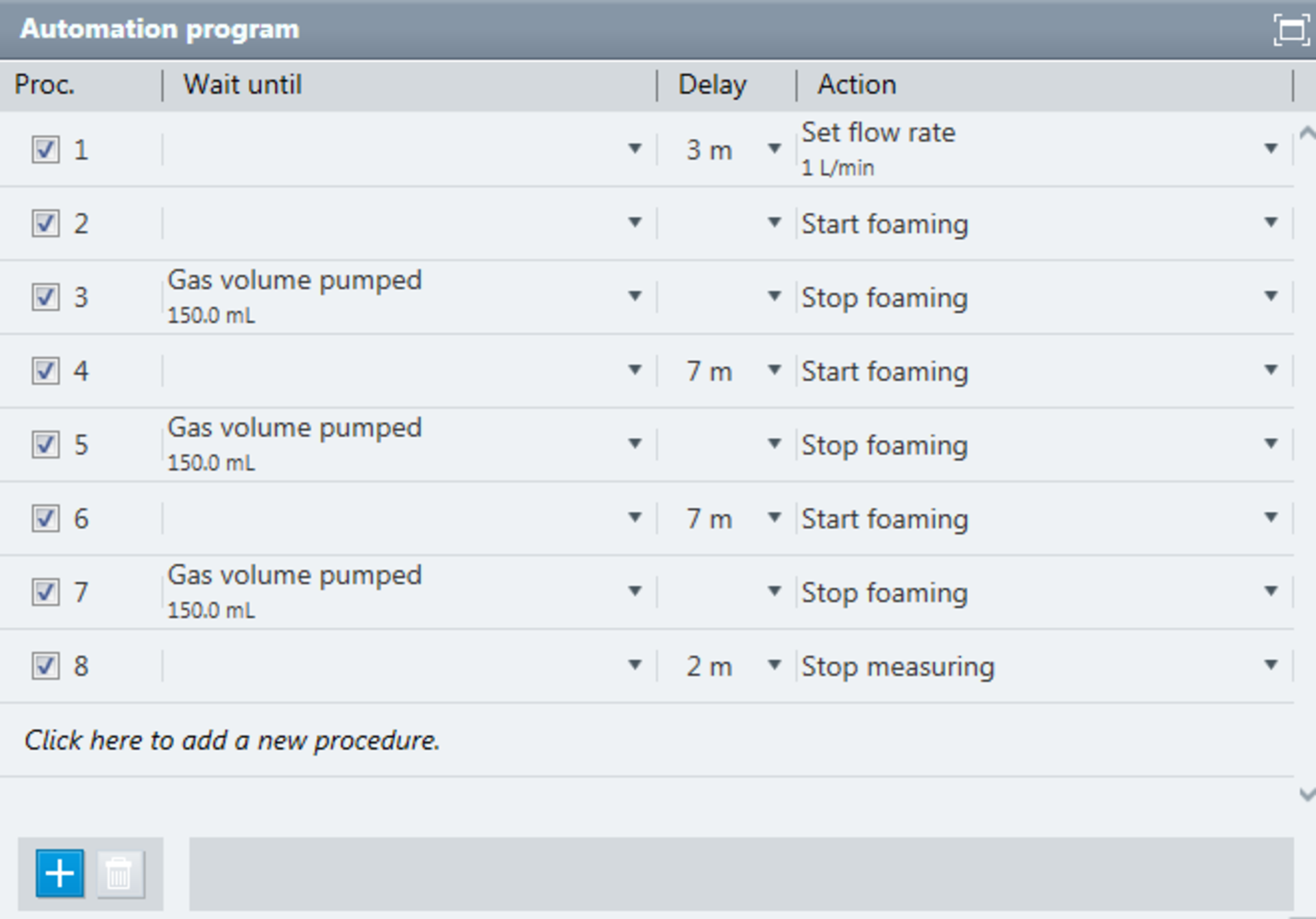
Results and Discussion
Figure 3 shows one exemplary set of raw data along with the detected liquid-air and liquid-foam boundaries for the used oil of Type B.
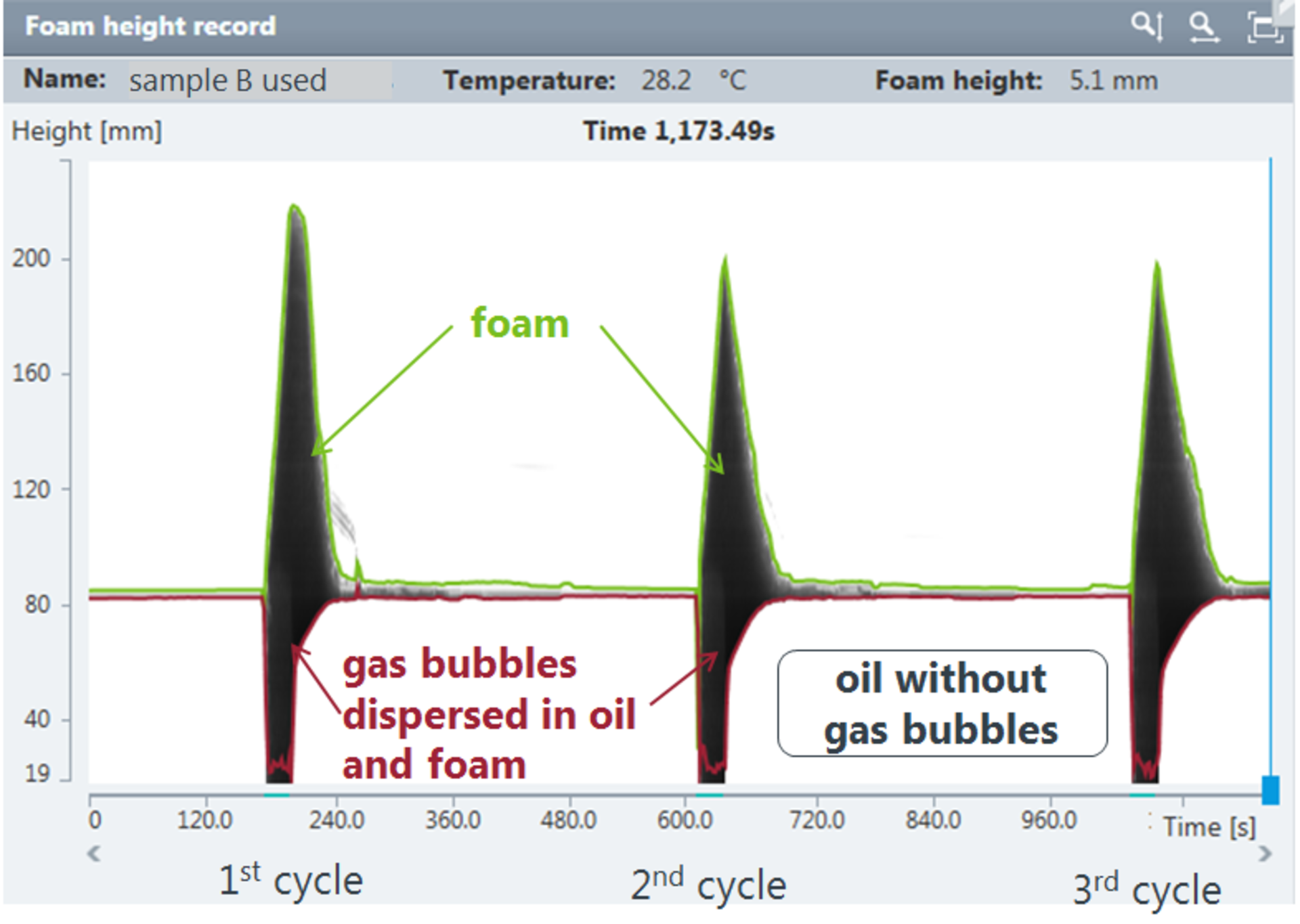
As can be seen the liquid was foamed up three times in a row. Each peak corresponds to the maximum foam height foam generated by introducing of 150 mL of air into the liquid. This foam quickly decayed and after a certain waiting time the same liquid was foamed up again. In Figure 3 we also labeled the two different gray parts in each cycle which originate either from pure foam or from tiny gas bubbles dispersed in the liquid beneath the foam. In between two consecutive cycles the liquid becomes transparent again and thus appears white in the raw data image.
For such low-foaming liquids we found that, in addition to the initial prewetting of the glass column, such measurements in cycles significantly increase the reproducibility of the detected foam height curves. This is because foam generation and decay can also be influenced by interactions of the liquid with the glass wall, in particular with its chemical and physical surface inhomogeneities. As can be seen in Figure 3 the maximum foam height for the first cycle is higher than for the second and third one. The measurements of the second and third cycle show a very high reproducibility. It also turned out that the sample-to-sample reproducibility was not perfect when looking solely at the first cycle but excellent when focusing on cycle number 2 and 3. This is shown in Figure 4, which displays the 2nd and 3rd cycle measured in two different experiments for fresh and used oil of Type A. For the oil of Type B we found the same quality of data (not shown here for the sake of simplicity). The first cycle of each experiment can be understood as a preconditioning / prewetting step of the glass column which guarantees the good reproducibility of the following cycles.
For both types of oil we found the determined total height in the 2nd and 3rd cycle is significantly higher for the used than for the fresh oil.
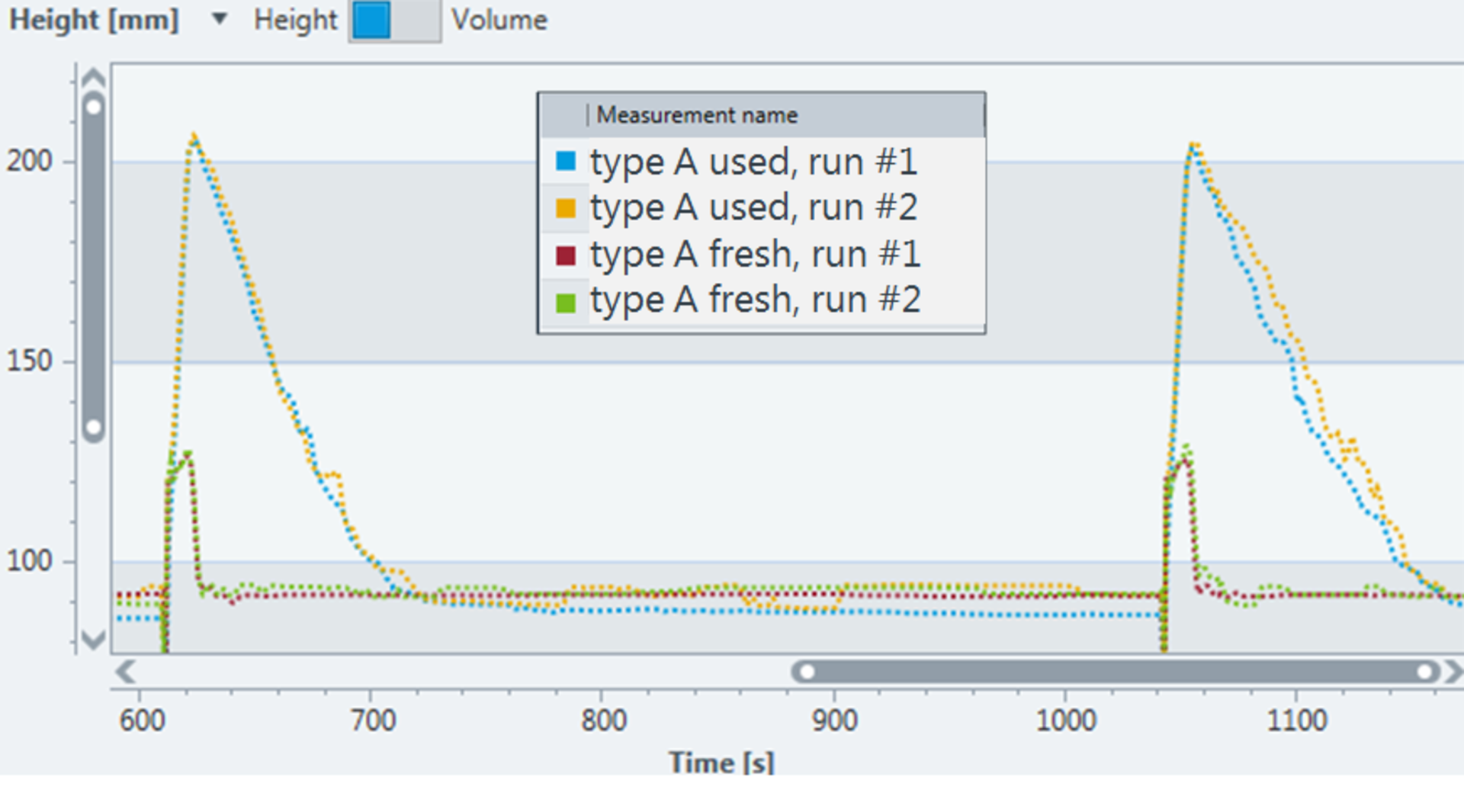
Figure 5 shows only one measurement for used and fresh oil of Type A and B. From this it can be seen that the curves for the fresh oils are very well comparable showing a very small amount of foam which instantaneously decays after the sparging of air has stopped. However, the used oils can be differentiated in terms of maximum foam height and speed of foam decay.
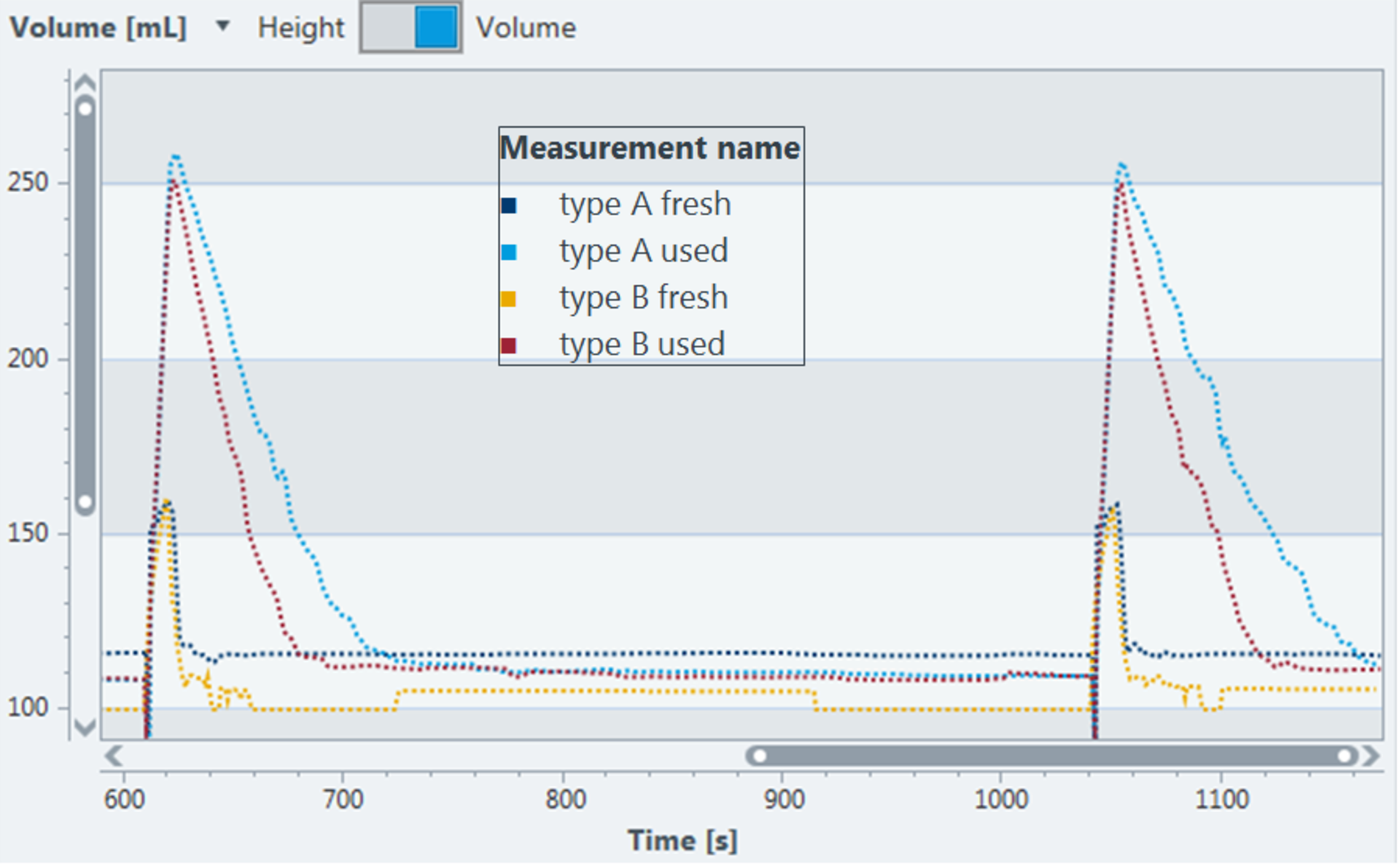
In conclusion, with the measurement procedure described here we present an experimental method which allows a reliable and highly reproducible differentiation between used and fresh samples of one type of oil and between different used oils. So far this was not possible by other experimental means and thus triggered the start of a larger study with the DFA100 at our client’s site comparing more than two different oils and states of usage. In that study our costumer uses a combined analysis of the detected maximum foam height and the relative decay time needed for the total height to decay to 10% of its maximum value. Based on the results of this study our costumer can now utilize a reliable experimental method for monitoring the usability of cooling liquids by measuring their foam behavior.
Summary
Using the KRÜSS Dynamic Foam Analyzer – DFA100 and sparging as foaming method we found a reliable experimental procedure to help one of our customers in monitoring the usage related changes of hydrocarbon based cooling liquids used in production machines. Each sample which is filled into the glass column of the DFA100 is foamed up three times consecutively with certain waiting times between each foaming cycle assuring that the generated foam fully collapses before the next foaming cycle. The first of those three cycles is used as a preconditioning / prewetting cycle. Only the maximum foam height and the determined time required for the foam to decay to 10% of its maximum value as deduced from the 2nd and 3rd cycle are used as result parameters characterizing the performance and/or usage state of the different cooling liquids. Using the procedure and result parameters described here our costumer now expands this study to more cooling liquids and for optimizing their process monitoring and production efficiency.
Bibliography
- [1] Katrin Oetjen, Christine Bilke-Krause, Mania Madani, Thomas Willers: Temperature effect on foamability, foam stability, and foam structure of milk. Colloids and Surfaces A: Physicochem. Eng. Aspects 460 (2014) 280–285
- [2] Investigating the foaming behavior of cooling lubricants and the effect of foam inhibitors (antifoams). KRÜSS Application Report AR279